Turning Lead in to Lithium:
Why just monitor when you can monitor AND manage for less?
The next ten years will be a decade of unprecedented change in the area of critical energy storage with new evolving battery storage chemistries and technologies.
The chemical battery remains the only method of supplying instantaneous electrical power.
For hundreds of years lead acid has been the established technology for this application but, on the brink of 2020, the questions surrounding the choice of a standby power source is no longer whose or what type of lead acid technology to use but which kind of chemical standby technology to use and this is coupled with the equally important question, of when would be the right time to switch if indeed it is decided to do so. The next few years will be interesting times indeed but are we really convinced that we have given our old friend (or arch nemesis) the lead acid battery, a fair and full opportunity at being the best that it can possibly be before we close the curtain on lead acid technology in critical power back-up forever?
This paper examines one philosophy that has not yet been generally embraced by battery companies involved with lead acid technology despite these ideas and techniques being commonplace (and in fact in many cases essential) with the new evolving technologies.
It seems that ultimately, our familiarity, the long heritage, reasonable cost, ease of recycling and relatively stable nature of lead acid chemistry has actually worked against it in this regard. The lead acid battery has increasingly been considered a commodity with price being the major factor above all else. All this at a time when it’s role in the supply of instantaneous power has become exponentially more important. Users have come to totally accept that operational life of lead acid batteries is around 50% to 60% of stated design life and that it is completely normal to replace them in a timescale even less than that to ensure there are no major problems. The commoditized nature of lead acid has allowed this norm to become the accepted philosophy with no serious interest in attempting to extend product life to its full potential. Perhaps the oncoming wave of new chemistries may encourage the lead acid industry (users and manufacturers alike) to begin to look at life extension techniques in order for them to remain competitive in critical power storage.
While it is generally accepted that some alternative battery chemistries require some form of electronic control and management the humble lead acid battery has soldiered its way to this point without any such innovation and in fact, many lead acid battery manufacturers have been somewhat suspicious of and resisted the inclusion of such technology.
At this time of the critical power market’s potential transition from lead acid to alternative chemistries, this paper seeks to explore a possible, practical, cost-effective option for extending the operational efficiency and life of the lead acid battery.
It is universally accepted that lead acid batteries last longest when kept at 77 degrees F and are maintained at their recommended float voltage. In some instances, for some manufacturers, these recommended float voltages are as precise as to be specified within +/- 1/100th of a volt. This critically important condition is relatively easy to maintain in a situation where battery units are used in single instances with their own dedicated constant voltage charger.
The fundamental fact remains however, that when lead acid jars are in a series string of more than one then each jars’ float voltage cannot be accurately controlled. Even with constant voltage charging and a string of identical make, model and batch number of jars, the variations in the battery manufacturing and chemistry mixing process causes each one to sit at different voltage levels.
This variation is the cause of two conditions within a string of lead acid batteries:
Overcharging
Undercharging
When a battery string is new these conditions are usually slight, however these slight variations grow in to ever increasing variations over time with increasing effect and these two basic conditions remain the inevitable root cause of the main failure modes within lead acid VRLA batteries over time:
Positive grid corrosion
Drying out
Sulfation
If this gradual but continuous under and overcharging can be eliminated then these failure modes can also be eliminated or at the very least greatly reduced.
This reduction leads to several other benefits:
A maximization of energy capacity within a string with an even distribution of energy.
Overall operational string life extension.
Reduced heating in jars that are being overcharged. This leads to less opportunity for electrolyte evaporation and in the case of VLA cells less frequent watering required.
Reduced stress on new spot replacements and subsequent reduced stress on older surrounding batteries.
Individual unit float voltage is also a hinderance to being able to realize the maximum capacity of a string. If a critical battery string is to maintain its design parameters then to all intents and purposes every series string of batteries has only the energy that is held within the smallest capacity or “runt” cell or jar within the string. Keeping all jars within a string to their maximum capacity ensures that the string will deliver the maximum energy it is capable of and prevent “stranded energy” within the string. When considering total string energy, a series of lead acid cells are in “lock step” with each other and although the voltage will increase with longer strings the amount of current it can supply remains only the amount of energy that is held within the cell that has the lowest charge capacity.
A battery care and management system (BACS) can “even out” this variation and can ensure that the maximum amount of energy is extracted from the string without undue stress or cell reversals occurring:
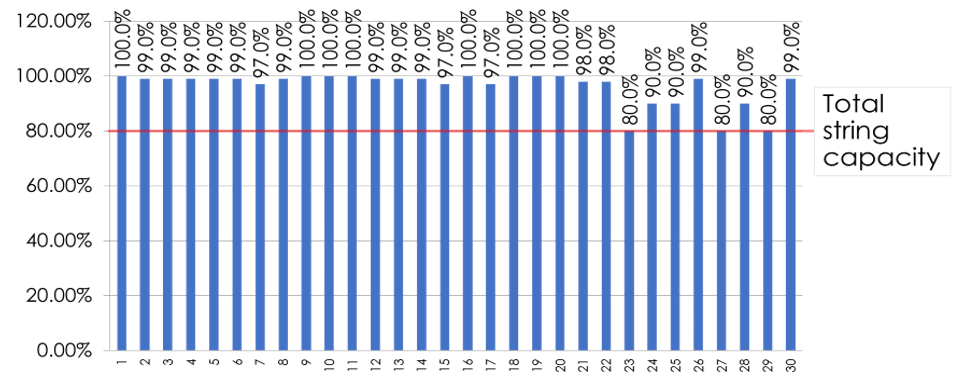
As well as evenly distributing energy across a string, tests conducted over time have shown that managing the individual float voltage of jars within a string reduces the rate of spot replacements.
Figure 2 shows a graph indicating the number of spot replacements by an independent third-party vendor at a datacenter colocation client over an eight-year period. Installation of a battery management system was commenced in 2011 and completed in 2012.
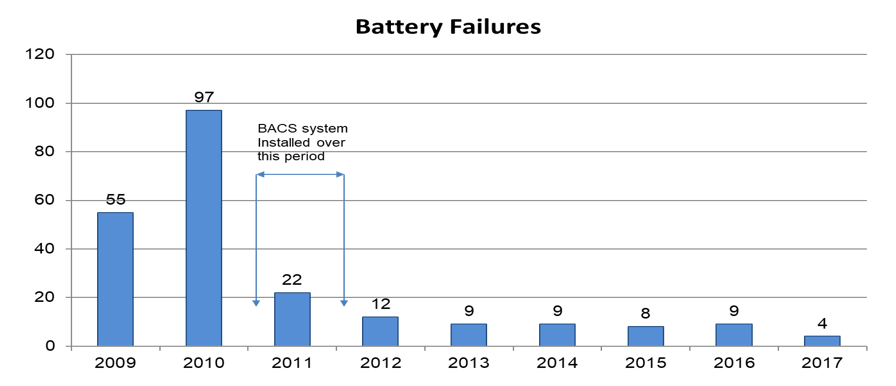
Despite the continual aging of the batteries and the number of battery systems increasing over the period from 10,000 to 15,000 over that time, the preventative maintenance reports show the number of spot replacements continually reducing over the 6 years that a BACS battery management system has been operating. (See figure 2).
Figure 3 below shows a manufacturers graph for the float service life of a small UPS VRLA lead acid battery.
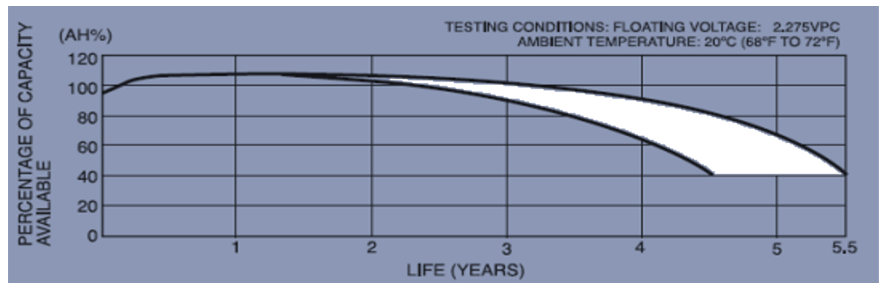
Three batteries of this type, two manufactured in 2012 (subjects A and B) and one manufactured in 2009 (subject C) have been float charged in a string configuration with a battery management and care system (BACS) installed on them throughout their entire operational life.
As can be seen from the graph the expected operational life of this battery type, down to 80% (normally considered end of life in UPS applications) is typically between 3.5 and 4.5 years with expected capacity after 4.5 to 5.5 years to be a relatively low 40% of the initial rated capacity.
These three test subjects were discharged down to 10.2 volts at the three-hour rate as highlighted on the manufacturers chart shown below:
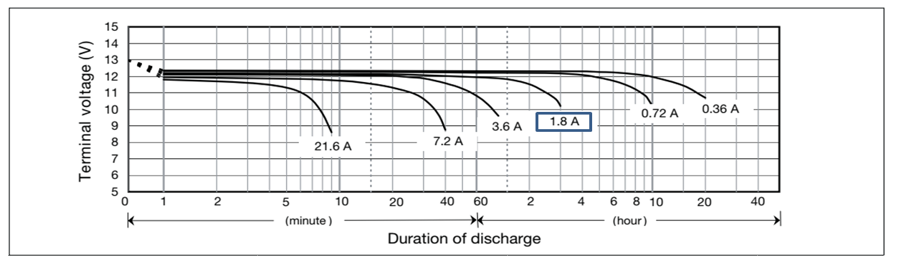
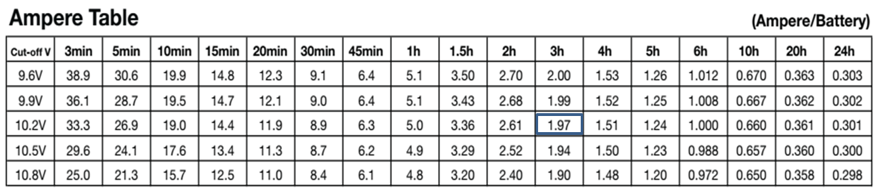
It can be seen from Figure 5 that capacity at the three-hour rate should be 1.97 x 3 hours = 5.91 Ah
Results of the discharge tests:
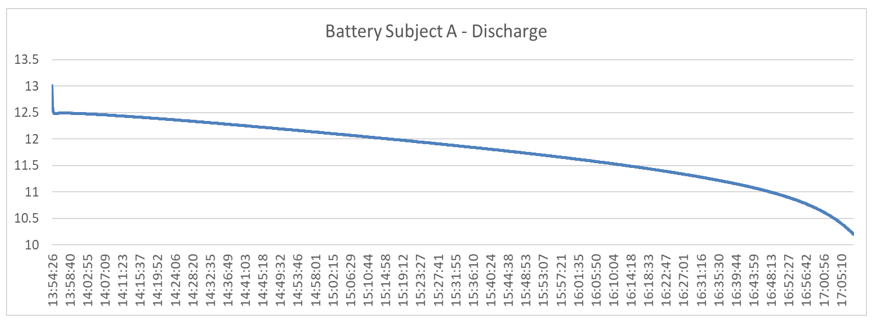
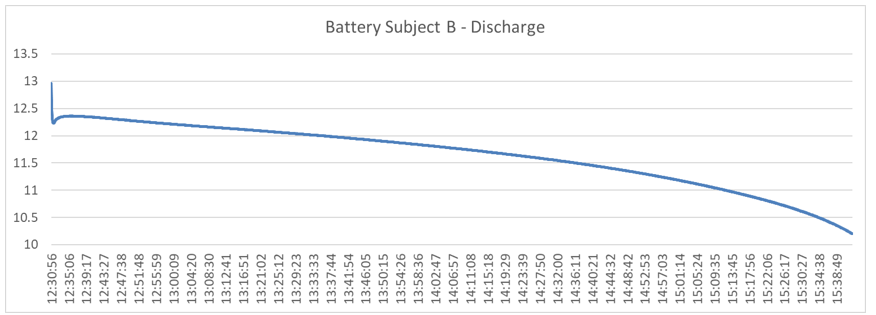
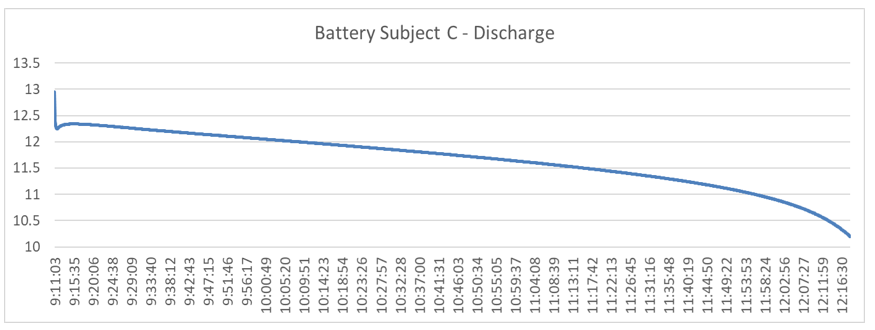
(Actual average current during the discharge test was over 1.80 amps @ 1.91 amps).
Subject A (6 years old) - Time to 10.2v was 3.23Hrs. Runtime % capacity = 108%
Subject B (6 years old) – Time to 10.2v was 3.21Hrs. Runtime % capacity = 107%
Subject C (9 years old) – Time to 10.2v was 3.13Hrs. Runtime % capacity = 104%
These results show that despite the percentage capacity available expected to begin to tail off after just over two years and rated capacity expected to be down to 40% at the end of life, these six and nine years old batteries are still delivering over 100% of their rated capacity with a BACS system managing them. Data over time has shown the balancing effect of BACS and its ability to manage and maintain float voltage to the manufacturer’s specification over the course of many years improves the battery’s ability to maintain discharge capacity and correspondingly can extend the useful service life of the battery.
Figure 9 below shows an independent study by the University of Berlin on the effects of the GENEREX BACS on sample lead acid cells. Results to date show a 4% to 5% efficiency increase with BACS compared to cells with no BACS installed over repeated discharges.
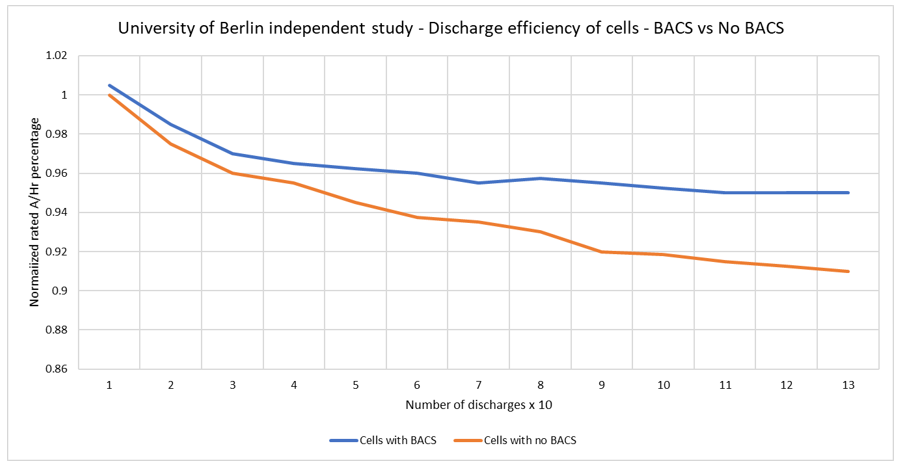
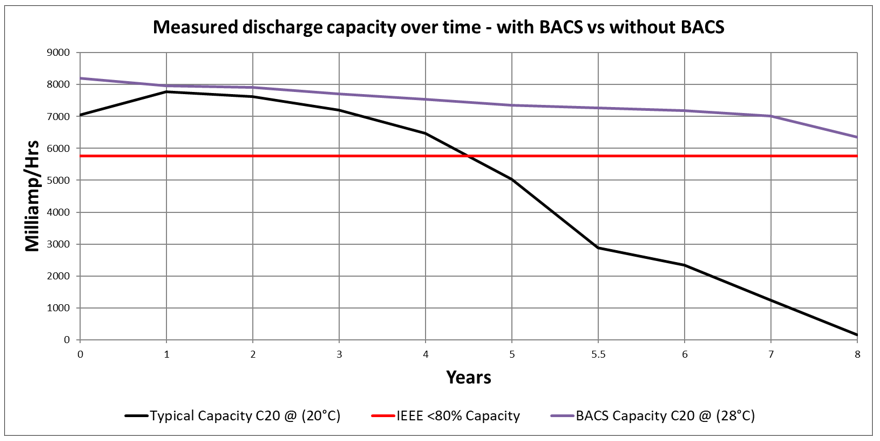
Conclusion:
The GENEREX BACS system was the first and remains the most accomplished and cost-effective battery management and care system of its kind. Costing less than most monitoring-only systems, BACS has been in continuous use throughout the world for over 14 years. Now in its third generation, using the BACS system on critical lead acid battery strings has consistently been shown to be beneficial to the performance and lifespan of the batteries it manages.
The common voltage imbalance of units within a string has always been an accepted norm. The low initial cost of the lead acid battery itself has made methods of countering this issue comparatively expensive and thus it has been generally ignored. Some attempts at extremely simple lower cost passive methods were made decades ago with very limited success and this limited success has been considered the “final answer” on the issue for some time now. That was then, but times have moved on. Ten years ago battery monitoring systems were considered a luxury.
Today they are accepted as a necessity for serious critical power battery systems with their use being recommended in established standards. Systems being deployed these days are reliable, accurate and dependable and monitor every aspect of a critical battery system, individual voltage, ohmic value, temperature, discharge current etc. GENEREX BACS gives all these things plus the added benefit of managing the float voltages to the optimal level according to the manufacturers specification. (BACS will also operate in harmony with temperature compensated charging systems). When considering a battery monitoring system, consider going one step further and having this hardware use all the information it gathers to actually actively control the condition of a critical battery string and optimize performance and life.
Before closing the door on lead acid technology completely, the time may be right to explore the benefits of adding or integrating a battery management system in order to improve the efficiency and the lifespan of the lead acid battery.
About GENEREX
GENEREX Systems Inc. Is based in Charlotte, NC and is a subsidiary of the high growth, worldwide GENEREX GmBH company which is based in Hamburg Germany and is the leader in SNMP UPS communications cards and server shut down software for the critical power industry.
All product sold in the US is designed for, manufactured and stocked in the US.
For further information:
704-966-1577
www.generex.us